3 in 1 sheet metal machine This Klutch® 3-In-1 Combination Sheet Metal Machine is a versatile combo unit that allows you to cut, bend and shape metal just the way you need it. The machine can shear up to 20-ga. mild . Exception: The equipment grounding conductor permitted in 250.146(D) shall not be required to be connected to the other equipment grounding conductors or to the box. (A) .
0 · woodward fab 3 in 1
1 · harbor freight metal brake shear
2 · grizzly 3 in 1 lathe
3 · 30 inch sheet metal shear
4 · 30 inch sheet metal brake
5 · 30 inch metal shear brake
6 · 3 in 1 metal brake
7 · 3 cylinder sheet metal rollers
As the name implies, pure waterjet CNC cutting involves cutting only with water. .
Smart 3-IN-1 machine will save you tedious sheet metal fabrication and finishing hours. The back gauge is used for repetitive work, significantly improving efficiency. This sheet metal brake is .This Klutch® 3-In-1 Combination Sheet Metal Machine is a versatile combo unit .
Flatten or form cylinders, cones, and arcs in sheet metal with ease using the slip roll .
sheet metal fabrication livonia mi
This Klutch® 3-In-1 Combination Sheet Metal Machine is a versatile combo unit that allows you to cut, bend and shape metal just the way you need it. The machine can shear up to 20-ga. mild .This compact and easy-to-use T21320 12" Combination 3-in-1 Sheet Metal Machine saves money and space by only requiring one tool to perform the job . Sorry I'm late in the conversation. A bit of history, the first 3-1 machine was introduced at the WESTEC machine tool show in Los Angeles over 35 years ago, it came from Japan and sold for over 00.00, it was a smash hit.. ALL 3-1 machines since have been produced in Asia. There are at least 5 Asian manufactures. It takes 2.3 tons of force to bend 1 foot of 16ga. mild steel across your 3/4" vee die. It takes 1.7 tons to force to bend 1 foot of 20ga. mild steel across your 3/4" vee die. Thats why those grease fittings are everywhere. My 3n1 is only a 20ga., capacity but after using it for years, you get a feel for its strength.
I use a thin cotter pin. Cut off long end even with short end. Bend ends over (about 1/4 inch). Open up a little bit so ends have pressure at the sides of the hole. Insert in hole, put in sheetmetal screw. Works great.
woodward fab 3 in 1
I need to bend up 2 sections that are about 14" long, 4" tall, and 3.5 wide. I'm replacing a section of unibody frame. It was a little thinner from the factory, but I have a sheet of 1/8 (maybe 11 or 12ga?) already. A little thicker is better in this case since the springs attach to it. I had one for close to 20 years and recently stepped up to a Miller 211. The sidekick is perfect for bodywork, sheet metal and mild fab work. My buddy bought it off me and uses it for the same purpose. In my opinion 1/4 steel is getting too thick for it but it will weld 1/8 no problem. Sent from my iPad using The H.A.M.B. mobile app

I like 20 gauge for patch panels. Easily shapable, easily weldable, and plenty strong enough for a body. You don't want the patches to be too rigid because you want to afford them the flex that the factory sheetmetal had. I live just minutes from them and a very good friend of mine works in the metal shop making panels. About 80% of their business is supplying other companies with products and the rest dealing with one single order here and there.
^This. Beads and bends will add stiffness, so you can use thinner metal compared to a mostly flat sheet with little or no support underneath. I used 16 gage flat sheet for a 24" x 43" trunk floor, but have two u-channel supports 12" apart in the center, and two smaller right angle iron pieces to help support the outer 18" or so.
As I describe what I did to my car (for ME, to DRIVE, not for "cheating" at car shows, but for ME), please keep in mind that there are many "delusional" car manufacturers such as Lotus, Avanti, Excaliber, and many others, and many many "delusional" boat factories that ROUTINELY embed things into their fiberglass-- metal windshield frames, metal . wondering the thicknes of sheet metal originaly used fore floor pans are they thicker than 18 gauge or thinner i want to use 16 gauge but hten it is realy hard to make beads in them . i would have to make a monster bead roller fore that . maby i will . but still what thicknes are you guys using fore replacing floor pans and other boddy parts
Sorry I'm late in the conversation. A bit of history, the first 3-1 machine was introduced at the WESTEC machine tool show in Los Angeles over 35 years ago, it came from Japan and sold for over 00.00, it was a smash hit.. ALL 3-1 machines since have been produced in Asia. There are at least 5 Asian manufactures.
It takes 2.3 tons of force to bend 1 foot of 16ga. mild steel across your 3/4" vee die. It takes 1.7 tons to force to bend 1 foot of 20ga. mild steel across your 3/4" vee die. Thats why those grease fittings are everywhere. My 3n1 is only a 20ga., capacity but after using it for years, you get a feel for its strength. I use a thin cotter pin. Cut off long end even with short end. Bend ends over (about 1/4 inch). Open up a little bit so ends have pressure at the sides of the hole. Insert in hole, put in sheetmetal screw. Works great. I need to bend up 2 sections that are about 14" long, 4" tall, and 3.5 wide. I'm replacing a section of unibody frame. It was a little thinner from the factory, but I have a sheet of 1/8 (maybe 11 or 12ga?) already. A little thicker is better in this case since the springs attach to it.
I had one for close to 20 years and recently stepped up to a Miller 211. The sidekick is perfect for bodywork, sheet metal and mild fab work. My buddy bought it off me and uses it for the same purpose. In my opinion 1/4 steel is getting too thick for it but it will weld 1/8 no problem. Sent from my iPad using The H.A.M.B. mobile app I like 20 gauge for patch panels. Easily shapable, easily weldable, and plenty strong enough for a body. You don't want the patches to be too rigid because you want to afford them the flex that the factory sheetmetal had.
sheet metal fabrication london
I live just minutes from them and a very good friend of mine works in the metal shop making panels. About 80% of their business is supplying other companies with products and the rest dealing with one single order here and there. ^This. Beads and bends will add stiffness, so you can use thinner metal compared to a mostly flat sheet with little or no support underneath. I used 16 gage flat sheet for a 24" x 43" trunk floor, but have two u-channel supports 12" apart in the center, and two smaller right angle iron pieces to help support the outer 18" or so. As I describe what I did to my car (for ME, to DRIVE, not for "cheating" at car shows, but for ME), please keep in mind that there are many "delusional" car manufacturers such as Lotus, Avanti, Excaliber, and many others, and many many "delusional" boat factories that ROUTINELY embed things into their fiberglass-- metal windshield frames, metal .

harbor freight metal brake shear
grizzly 3 in 1 lathe
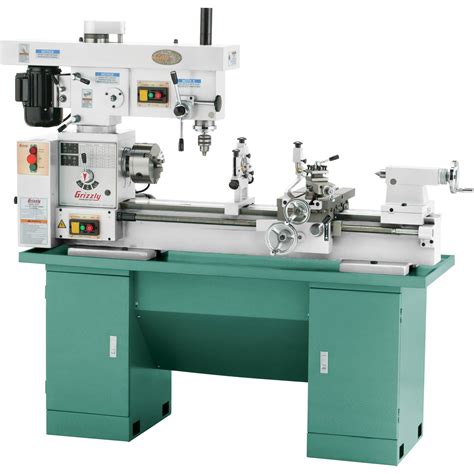
sheet metal fabrication jobs birmingham
30 inch sheet metal shear
Logically, in order to through a box junction, you must, at some point, enter the box. However, when turning left, you should only do so once your exit path is clear and you can cross the junction without having to stop.
3 in 1 sheet metal machine|3 cylinder sheet metal rollers